2.1. Shopfloor-Management
Als Lean-Management um die 2000er-JAhre modern wurde war die Intention von Shopfloor-Management die "Rückbesinnung" auf die Wertschöpfung und die Mitarbeiter.
Mit Shopfloor-Management (SFM) wird der regelmäßige (tägliche) Informationsaustausch mit den Mitarbeitern sichergestellt und eine Transparenz über den Leistungsgrad erreicht.
Um dieses zu leben muss eine Organisationstruktur geschaffen werden welche den täglichen und strukturierten Austausch ermöglicht. Hierzu sind unter anderem Kennzahlen notwendig, welche den Leistungsgrad der Organisation zeigen. Durch die Regelkommunikation wird der durchgängige und strukturierte Informationsfluss vertikal zw. Wertschöpfungs- und Unterstützungsprozess als auch horizontal entlang der Hierarchiestufen verstanden. Für die Einführung und Aufrechterhaltung von Standards (auch Einhaltung von Produktionsparametern) sowie zur Evaluierung des gelebten Standards, können Arbeitsplatz-Checks durchgeführt werden.
Organisationsstruktur
Wie vermutlich bereits bekannt hat die Organisationsstrukturierung Einfluss auf die Aufgabenorganisation und umgekehrt. Fertigungs- und Montagebereichen sind meist Linienorganisationen. Ein Mitarbeiter hat eine direkte Informations- und Weisungsbeziehung zu einer Führungskraft. Wobei eine Führungskraft mehrere Mitarbeiter führt. Ein alter Grundsatz der Organisationslehre sagt, dass eine Organisationseinheit im Idealfall zwischen 5 und 10 Mitarbeiter hat und nicht 15 Mitarbeiter überschreiten sollte. Wichtig ist, dass die Mitarbeiter einen Ansprechpartner haben. Im Bereich der Produktion (wertschöpfenden Tätigkeiten) hat die erste Ebene meist „nur“ fachliche Führungsaufgaben und arbeitet ebenfalls aktiv wertschöpfend. Wie diese erste Ebene genannt wird unterscheidet sich sehr stark. Ein altmodischer Begriff ist Vorarbeiter, moderner ist der Teamleader häufig werden auch japanischer Begriff verwendet. Nach der ersten Ebene – Vorarbeiter – kommt die Meister- oder auch Abteilungsleiterebene, je nach Organisationsgröße.
Zu Beginn dieses Absatzes habe ich beschrieben, dass die Aufgaben klar strukturiert sein müssen. Es muss definiert sein, was haben Mitarbeiter, Vorarbeiter, Meister etc. zu tun und wo sind die Abgrenzungen – Stichwort Schnittstellenmanagement – zu anderen Bereichen. Wenn dies nicht erfolgt kann es zum Beispiel sein, dass der Meister regelmäßig irgendwelche kommissionierten Umfänge durch die Hallen mit einem Hubwagen schiebt. Das ist aber sicher nicht die originäre Aufgabe eines Meisters (außer vielleicht in Kleinstbetrieben).
Kennzahlen
Kennzahlen sollen zur Transparenz und schnellen Entscheidungsfindung/Abstimmung beitragen. Diese können ein Bestandteil des Visualmanagement sein. Kennzahlen welche im Shopfloor Management angewendet werden, sollten robust sein. Das heißt für mich, dass die Kennzahlen einfach zu erfassen, keine lange Analyse/Auswertung benötigen und klar und (einfach) verständlich sind. Kennzahlen welche für die erste Ebene relevant sein könnten sind, anwesende und abwesende (z.B. kranke) Mitarbeiter, Auslastung/Output des vorherigen Tages und die geplanten Mengen des aktuellen Tages.
Regelkommunikation
Wichtig für das Shopfloor Management ist, dass es regelmäßig und mit gleichbleibenden Teilnehmern stattfindet. In den meisten wertschöpfenden Bereichen findet es am Morgen statt. Durch eine klare Strukturierung der Besprechung wird die Effizienz sichergestellt. Die Dauer der Besprechung sollte 20 bis 30 Minuten nicht überschreiten. Die Teilnehmer und wichtige Themen sollten dokumentiert werden. Häufig werden die Besprechungen im Stehen durchgeführt. Alle Teilnehmer sollten darauf achten pünktlich zu sein à Verschwendung (Wartezeit) reduzieren.
In der ersten Eben werden die Arbeitsaufgaben und Aufgabenteilung innerhalb der Gruppe mit den Mitarbeiter, Vorarbeiter oder/und Meister besprochen. Hier werden von dem Meister die wesentlichen Kennzahlen von den Mitarbeiter abgefragt (z.B. Auslastung, Output, etc.). Etwaige Herausforderungen des vorherigen Arbeitstags sowie mögliche Fehlerursachen und Lösungsansätze werden besprochen. Je nach Erfahrungsstand werden z. B. Ichikawa-Diagramme oder auch A3-Lösungsformular von den Mitarbeitern vorerfasst. In dieser Runde können auch wenn vorhanden Themen für des kontinuierliche Verbesserungsprozesses besprochen werden.
Der Meister nimmt die offenen Themen, Kennzahlen und positive Ereignisse mit in die das Gespräch der nächsten Ebene des Shopfloor Management. Die Teilnehmer dieser Ebene sollten die Meister des Produktionsbereiches sein inkl. dem Produktionsleiter sowie die Leiter/Verantwortlichen der Schnittstellen der wertschöpfenden Bereiche sein. Als Lieferanten können dies Logistik, Einkauf und Instandhaltung; als Kunden z.B. der AfterSales-Bereich oder die Montage sein. Auch bei dieser Besprechung geht es um operative Themen welche aktuell anliegen und über welche informiert werden muss bzw. welche einer Lösung bedürfen.
Arbeitsplatzcheck
Erreicht werden soll durch den Arbeitsplatzcheck eine kontinuierliche Prüfung des aktuellen Status im Produktion-/Fertigungsbereich. Verbesserungspotentiale und notwendige Korrekturmaßnahmen sollen schnell erkannt und abgestellt werden.
Der Arbeitsplatzcheck ist im Prinzip ein kleines Audit, das folgende Eigenschaften hat:
- Es wird in kurzen Abständen (täglich) durchgeführt
- Es werden max. 10 Fragen abgeprüft
- Es ist bereichsspezifisch
- Es soll motivieren und nicht kontrollieren werden
- Es werden die Mitarbeiter Vorort über das Ergebnis informiert
- Es wird sich ständig verbessert
- Es ist interdisziplinär
Zu 1 – tägliche Durchführung des Arbeitsplatzcheck
Wie Eingangs geschrieben kommt es auf die Kontinuität an. Daher ist es sinnvoll den Arbeitsplatzcheck täglich durchzuführen. Hierbei sind selbstverständlich die Gegebenheiten vor Ort zu berücksichtigen. Wenn in einem Produktionsbereich 3 schichtig an 10 Arbeitsplätzen gearbeitet wird ist ein täglicher Rhythmus sinnvoller als bei einem Einzelarbeitsplatz bei welchem nur 1 schichtig gearbeitet wird.
Wenn wir bei unserem Beispiel mit den 10 Arbeitsplätzen bleiben (z. B. verschiedene Metallbearbeitungsmaschinen), führe ich jeden Tag an einer zufällig ausgewählten Maschine den Arbeitsplatzcheck durch. Mit etwas Übung und praxisorientierten Fragen, geht der Arbeitsplatzcheck keine 5 Minuten.
Zu 2 – 10 Fragen
Wie bereits oben geschrieben, sollten die Fragen praxistauglich sein, d.h. in einer einfachen, klaren verständlichen Sprache definiert sein. Der Mitarbeiter Vorort muss es verstehen und nicht der Vorstandsvorsitzende beeindruckt werden.
Durch die Fragen sollen definierte Standards, z. B. für Ordnung und Sauberkeit oder qualitätsbezogene Abläufe geprüft werden:
- Sind die Standards bezüglich Arbeitssicherheit und Umweltschutz eingehalten?
- Wurde die Erststückfreigabe durchgeführt?
- Erfolgen regelmäßige die Werker-Selbstprüfungen?
- Stimmen die IST-Maschinenparameter mit den SOLL-Vorgaben überein?
- Entspricht das Vormaterial den Arbeitspapieren?
- Ist der aktuelle Fertigungsauftrag im BDE-System angemeldet?
- Wurde die Emulsion am Vortag geprüft?
- Wurde die autonome Instandhaltung durchgeführt?
- …
Die Fragen sollten auf eine DIN-A4-Seite passen. Die Bewertung sollte durch ein JA oder Nein bzw. 0 oder 1 erfolgend können.
Für wichtige Fragen, wie Thema Arbeitssicherheit und Umweltschutz oder auch das richtige Vormaterial müssen bei einer Abweichung direkt auf ein nicht bestehen (roten) des Arbeitsplatzcheck führen. Bei roten Ergebnisse sollte die Abweichung schnellstmöglich abgestellt werden und der Arbeitsplatz/-bereich am Folgetag nochmals überprüft werden mittels des Arbeitsplatzcheck.
Zum Abschluss der Fragen muss eine Bewertung stattfinden. Das Ergebnis kann in Ampelfarben (grün, gelb, rot) visualisiert werden. Für die Einführung sollte die Punktezahlen für die einzelnen Farben so gewählt werden, dass nicht dauernd ein rotes Ergebnis erreicht wird. Auch hier handelt es sicher um einen Veränderungsprozess und die Mitarbeiter müssen „mitgenommen werden“. Dies erreicht man eher durch gelbe und grüne Ergebnisse, als wenn ich den Mitarbeitern suggeriere sie machen alles falsch.
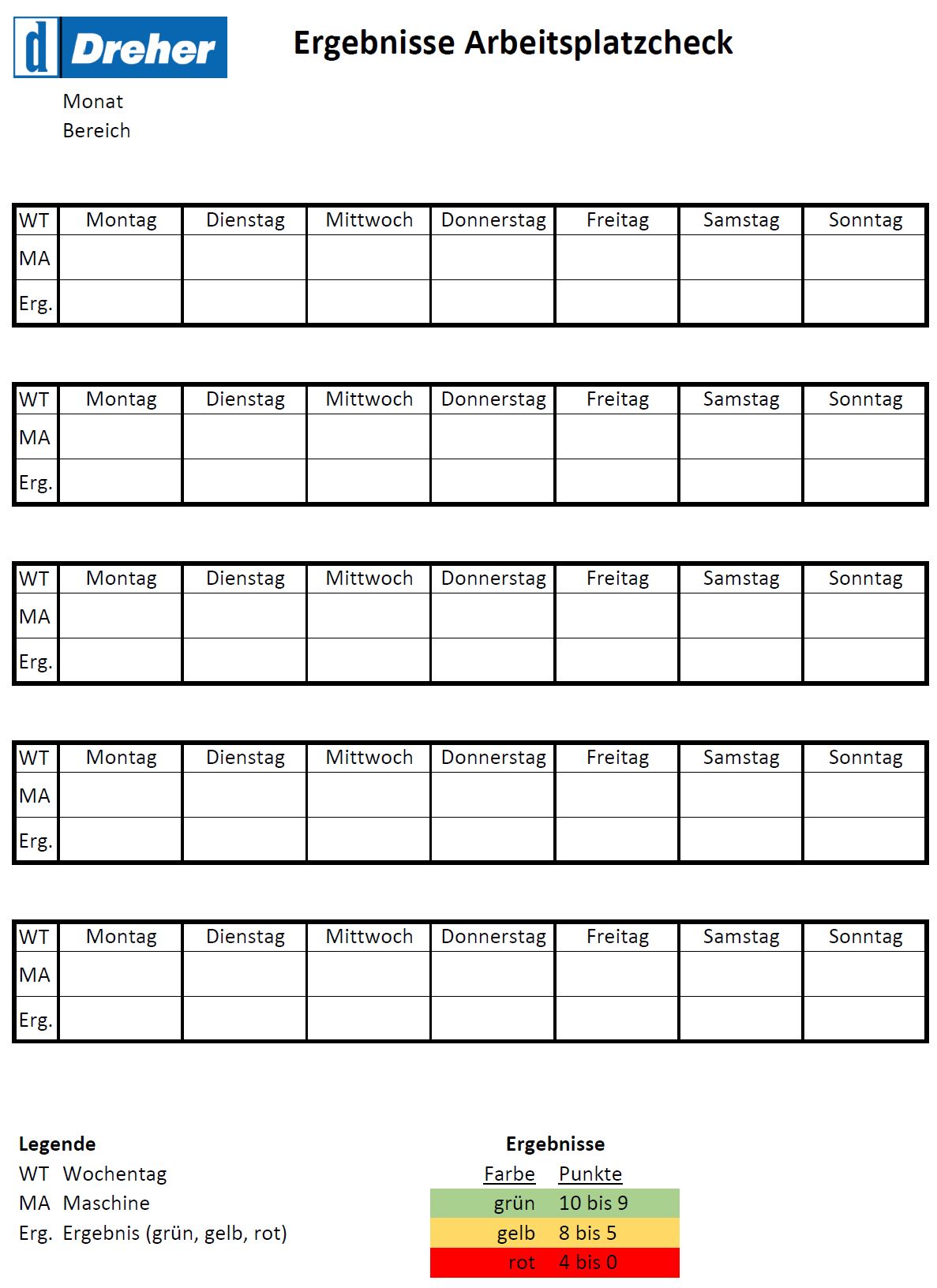
Zu 3 – Bereichspezifisch
Die Fragen welche gestellt werden, sollten auf den jeweiligen Arbeitsbereich passen. So macht es z. B. wenig Sinn bei einer Druckmaschine die Emulsion zu prüfen.
Zu 4 – Motivieren nicht Kontrollieren
Durch die Einbindung der Mitarbeiter Vorort und der Fragen auf den jeweiligen Bereich soll eine motivierende Wirkung für die Mitarbeiter entstehen. Wertschätzung, Offenheit, Kontinuität und Dialog dies motiviert die Mitarbeiter. Wichtig es geht nicht darum Fehler zu finden, sondern darum sich stetig zu verbessern. Es ist ein Marathon kein Sprint.
Zu 5 – Mitarbeiter informieren über Ergebnisse
Wie oben bereits benannt geht es um die Einbindung der Mitarbeiter, den Dialog. Die Mitarbeiter müssen über den Sinn informiert und eingebunden werden. Werden Abweichungen erkannt, so muss der Mitarbeiter informiert werden. Wichtig ist hier auch den möglichen Grund (in Stichworten) zu dokumentieren.
Zu 6 – Ständige-Verbesserung
Die ständige Verbesserung wird einerseits durch die Wiederholung in kurzen Abständen und die Einbringung der Mitarbeiter erreicht. Ein Weiterer wichtiger Punkt ist aber auch die Visualisierung und Dokumentation.
Bei der Durchführung festgestellten Abweichungen können wenn möglich umgehend von den Mitarbeitern, Vorgesetzten, Kollegen (z.B. Instandhaltung, Qualitätsmanagement) behoben werden. Die Mitarbeiter vor Ort sollen sehen, dass sich um die Abweichungen gekümmert wird. Relevante Themen können auch innerhalb der Regelkommunikation kommuniziert und eskaliert werden.
Für das nachhaltige Verbessern ist es wichtig, dass die festgestellten Abweichungen dokumentiert werden. Bei ist entscheidend, dass der Fehlergrund (welche Frage) und Fehlerort (welcher Arbeitsplatz) festgehalten werden. Dadurch können Schwerpunkte monatlich oder vierteljährlich nachgehalten und visualisiert werden.
Zu 7 – Verschiedene Blickwinkel erschaffen neu Perspektiven
Der Arbeitsplatzcheck betrachtet den Arbeitsplatz aus mehreren Betrachtungswinkeln, Qualität, Arbeitssicherheit, etc. Aus diesem Grund ist es sehr sinnvoll die unterschiedlichen Bereiche (Unterstützungsprozesse) in den Arbeitsplatzcheck einzubinden. Dies bietet die Chance die unterschiedlichen Sichten zu nutzen. Der Instandhaltungsleiter wird den Arbeitsplatz anders betrachten als der Leiter des Qualitätsmanagement. Hierdurch können nicht nur Verbesserungspotentiale am Arbeitsplatz sondern auch den jeweiligen Unterstützungsprozessen (Dokumentation, Stammdatenqualität) festgestellt werden.
Wie unter 1 bereits geschrieben, sollte der Arbeitsplatzcheck „im eingeschwungenen Zustand“ nicht länger als 5 Minuten dauern. Aus diesem Grund macht es aus meiner Sicht wenig Sinn, wenn 5 bis 6 Mitarbeiter gleichzeitig den Arbeitsplatzcheck Tag für Tag durchführen. Es macht Sinn z. B. in einem 14 Tagesplan die verschieden Kollegen festzulegen welche den Arbeitsplatzcheck durchzuführen haben.
Mögliche Teilnehmer welche je nach Unternehmensgröße variieren können:
- Meister des Fertigungsbereichs
- Planungsmitarbeiter
- Instandhaltungsleiter
- Qualitätsleiter oder Qualitätsmitarbeiter
- Sicherheitsfachkraft
- Geschäftsführung
- Vertriebsleiter oder Vertriebsmitarbeiter welcher für den Bereich arbeitet.
Verwandte Themen
Schnittstellen zu anderen Lean-Schlagwörtern:
- Gruppenarbeit
- Visualmanagement (Kennzahlen)
- Gemba Walk