Prozessdefinition - SOLL-Modellierung
Auf Basis der IST-Analyse werden nun der Prozessablauf verändert.
Grundlegend erfolgt die Verbesserung nach folgenden Gesichtspunkten:
- wertschöpfende Prozessschritte werden optimiert.
- unterstützende Prozessschritte sind zu optimieren und zu parallelisieren
Arbeitsplanung, Beschaffung, Rüstvorgänge, Werkzeugbereitstellung, Reinigungstätigkeiten, ... - nicht wertschöpfende Prozessschritte sind soweit möglich zu eliminieren
Nacharbeiten, Qualitätsprüfungen, Redundanzen, Nachfragen, ...
Eine starke Aufmerksamkeit sollte auf die Einflüsse der Prozessschritte gelegt werden. In der Menge dieser Einflüsse sind die Probleme eine Untermenge und sind in geeigneter Form durch die Modellierung zu beheben.
Eine Möglichkeit diese Probleme zu analysieren bietet das ISHIKAWA-Diagramm. Sehr wichtig ist dabei, nicht zu früh aufzuhören bei der Ursachenanalyse. So kann das Fehlen von Bauteilen auf der ersten Ebene auf zu späte Lieferung durch den Lieferanten begründet sein. Wenn man dies weiter untersucht könnte herauskommen, dass die Wiederbeschaffungszeiten zu gering sind, oder falsche Mindestbestände bestehen, oder oder oder. Auch diese angeführten Gründe sind noch weiter herunterzubrechen. Grundlegend sollte mindestens fünf Mal mit WARUM gefragt um den (wahren) Grund eine Ursache zu ermitteln.
Wichtig ist auch die Berücksichtigung des Informationsflusses. Diese sollte in eine Richtung erfolgen. Reziproke Informationsflüsse sind zu vermeiden. Soweit möglich sollten die Schnittstellen vor allem zwischen Unternehmensbereichen (Abteilungen) schriftlich in Form von Datenbanken, Excel- oder Worddateien erfolgen. Zu vermeiden sind verbale und nicht standardisierte Informationsaustausche. Durch die Standardisierung kann eine Harmonisierung und damit eine Verbesserung erreicht werden.
Es sind auch die Prozesswerte zu überprüfen und wenn notwendig neu zu definieren. Wichtig ist, dass die Prozesskennwerte einfach, schnell und dauerhaft zu ermitteln sind.
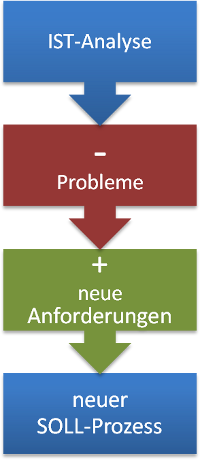